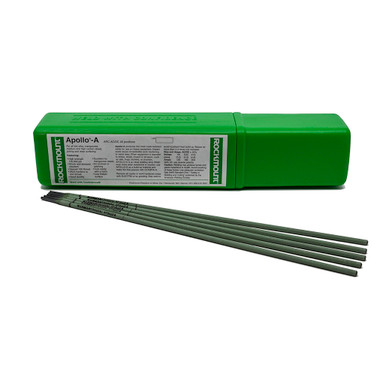
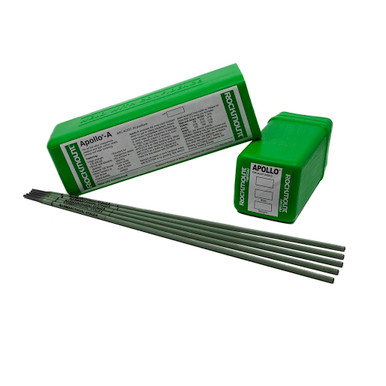
Apollo A Arc Rod
SKU: RM-1004For joining, build-up and wear surfacing of all low alloy, manganese, medium and high carbon steels. Apollo A has been developed to produce the most crack resistant welds for use on heavy equipment. Under impact, Apollo A work hardens considerably to resist wear. In addition, this alloy has extraordinary strength combined with excellent ductility (30% elongation). It is superior for metal-to-metal wear applications.
When equipment is exposed to stress, shock, impact or abrasion, Apollo A is an ideal welding material. Outstanding results are found on all critical joints and when impact is present as in rails, frogs and cross overs. Use for manganese wear plates, buckets, crushers, hammers, dragline chains and pins.
When even more wear resistance is required, final passes should be made with our Olympia, Omega or Zeta hard face alloys. Download PDF
Features
Shock and Abrasion Resistant
Deposit 185 Brinell (11 RC)
Work Hardens To 55 RC
Cuts Easily With A Torch
Excellent For Manganese Steels
No Pre-Heat Or Peening
Flux Coating Not Affected By Moisture
Good Ductility
Low Friction Surface
Applications
For use on rails, frogs, and crossovers.
Also for use on manganese wear plates, buckets, crushers, hammers, dragline chains and pins.
Recommended Settings
Recommended Settings:
1/8” Diameter – 120 amps
5/32” Diameter – 160 amps
3/16” Diameter – 200 amps
Best Practices
Skip weld to avoid localized heat buildup.
Weave no more than 2 to 3 times rod diameter.
MSRP: